Session 4: Innovative Automated NLT Fabrication Techniques for Timber Buildings
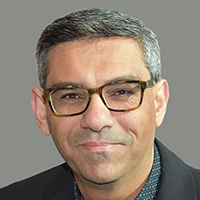
Sobhy Masoud
Principal
Stephenson Engineering Ltd., Toronto
An automated fabrication technique has been implemented for the fabrication of nail-laminated timber (NLT) panels to reduce the cost-of-labor and improve the quality of the panels. The automated procedure has been developed to progress from an old, manually-fabricated building component, to one which has now been analyzed using modern engineering techniques and testing. Much of the work involved in fabricating NLT panels is repetitive and the manually fabricated method of nailing dimensional lumber is labor-intensive. The variations in lumber, different nailing patterns, different lay-up patterns and the use of consistent rectilinear shapes are all important variables to consider during the fabrication of NLT.
The best way to control these variables while increasing the production time per square foot/meter is to use automation. An entire NLT panel can be fully fabricated using new automated techniques in approximately 50 minutes, including post-production application of waterproofing membranes or surface pre-finishing if required. The cost of mechanizing the process of fabricating NLT is a justifiable investment due to the increased popularity and use of NLT for single and two-span continuous floor and roof applications and its structural capacity benefits compared to cross-laminated timber (CLT) wood panels. The structural panel capacity is related to the type of connection used (butt-jointed or continuous) along with lamination nail-spacing and quantity. Implementing this technique has enabled an estimated 200 NLT panels to be installed on a timber-frame project in Toronto, leading the way for fast, green, and aesthetically-pleasing building design that is economically competitive.