Session 7: Space as Product: High-Rise Modular Construction as a Way Forward
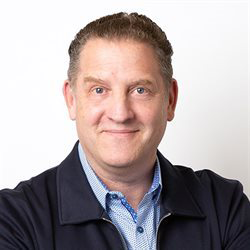
Timothy Johnson
Partner
NBBJ, New York City
At a time when building construction efficiency has decreased by 4 percent since the 1960s, efficiency in automotive manufacturing has increased by 400 percent, largely due to implementation of robotic manufacturing. The world needs to build 2 billion new homes over the next 80 years (that's 25 million per year). Worldwide automotive production hit 73.5 million units in 2017.
A new construction paradigm needs to be created to increase efficiency, improve quality, and reduce cost for the millions of houses that need to be produced in developing countries around the world. With the advancements in autonomous vehicles, the number of cars manufactured on the planet will begin to decline by 2030. Learning from the manufacturing processes of the automotive industry, modular high-rise housing should be built using robotics and mass production, not unlike the automotive industry.
This presentation explores the use of potential “spare capacity” of automotive manufacturing facilities to create high-density, high-rise housing modules. It explores technical aspects such as materiality and process, and also explores making modular construction more design-oriented in terms of creativity and flexibility, and more humane and choice-centered for its inhabitants. In order for the design and construction industry to advance to meet the needs of today and tomorrow, it needs to radically change. Modular construction can be that change. This presentation shows viable solutions around modular, in terms of method/process, materiality, typology, and the human experience.